Hydraulic dampers
With mechanical movement, an after-movement or a sound may occur at the end of the motion. For example, a steel rubbish bin slamming shut. A steel valve will move back due to the impact and strike again, and it will generate a lot of noise.
To dampen this impact you can use a hydraulic damper as a final buffer. Wherever a movement is made, in which mass reaches an end position uninhibited, a hydraulic damper can be a good solution. Examples of these applications are:
- Rotary movement, horizontal and vertical
- Falling masses, linear or rotating
- Horizontal linear movement
- End of a conveyor track
- Overhead crane
- Emergency stop AGV
- Cylinder final damping
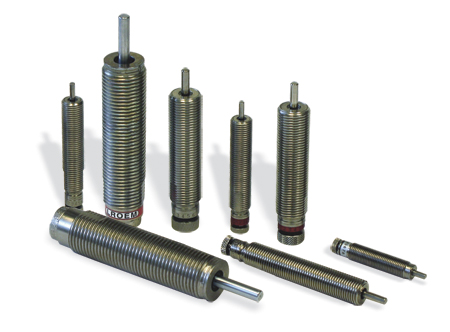
How does a hydraulic damper work?
A hydraulic shock absorber converts the kinetic energy of the movement into thermal energy by pressing the oil through small holes (orifices). This causes the motion to dampen out and the mass will eventually reach its final location without speed. The impact is soft and quiet due to this damping, which is important for the lifespan of the components. In addition, it is more pleasant for the environment. The damper returns to its starting position by a spring or other compensating volume.
Types of hydraulic dampers
There are various hydraulic dampers, each with their own advantages. The most common shock absorbers are described below.
Adjustable shock absorbers
Adjustable hydraulic dampers can be adjusted in terms of damping to achieve optimal shock absorption. If the application has exactly the same speed and mass to stop every time, this is a good way to optimize this movement. With adjusting with the adjustment button, you'll secure these hydraulic shock absorbers. The setting is saved.
Fixed shock absorbers
Fixed hydraulic dampers can be used more widely and under varying conditions in terms of masses and speeds. Hence the reason why these dampers are also called self-compensating dampers. Even if hydraulic dampers work in parallel to slow down a larger object, non-adjustable dampers are recommended. In terms of movement profile, the damping can also help to reduce the number of G-forces through a constant deceleration; a progressive decrease in speed.
Oil brake cylinders
Oil brake cylinders maintain a constant speed of motion by passing the oil through a needle control valve. Thanks to the adjustable constriction, you create a constant flow through the needle control valve and the speed becomes constant. This can be done, for example, with movements in which you do not want the object to come down at high speed due to gravity, or by limiting the speed of a pneumatic cylinder. These are not end buffers, but work the entire stroke. The cylinders can also be used in inward or outward stroke or a 'free-flow', thus the speed is unlimited in one direction.
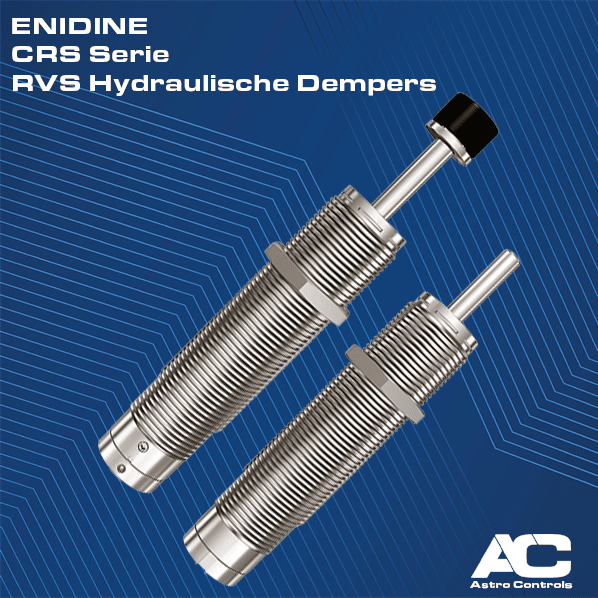
Purchasing hydraulic dampers
Curious how we can help you choose the right dampers? contact us to talk to one of our specialists.